Purpose-Built Monitoring Solutions for Energy, Power, and Heavy Industry
Monico Monitoring supports critical industries with tailored remote monitoring, data acquisition, and IIoT solutions designed for harsh environments and high-value equipment. Whether you’re in oil and gas, mining, electric power generation, or marine operations, our systems deliver real-time machine data, predictive insights, and seamless integration with enterprise platforms—helping you reduce downtime, optimize maintenance, and improve asset reliability.
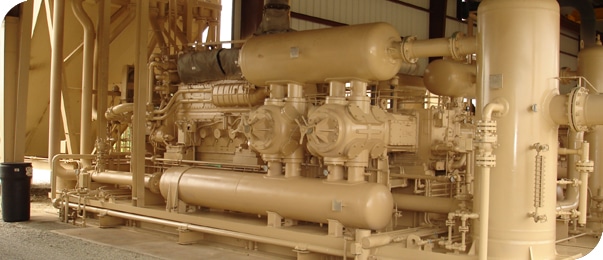
Oil & Gas
From upstream drilling to midstream transport and downstream refining, Monico’s monitoring systems provide real-time visibility into critical oil & gas equipment. Our rugged solutions support remote operations, harsh conditions, and help prevent costly unplanned downtime.
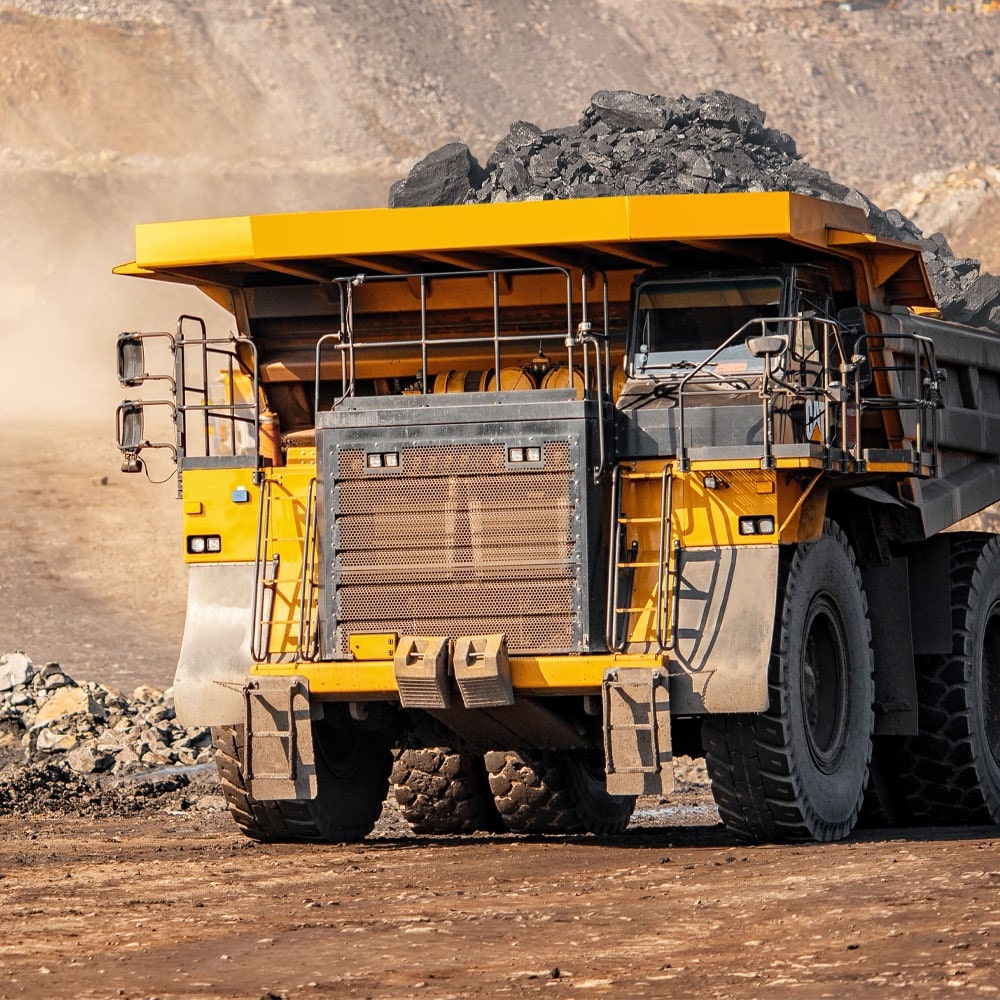
Mining
Built for high-impact environments, Monico’s solutions help mining operations monitor haul trucks, crushers, generators, and more—improving asset reliability and enabling predictive maintenance across the mine site.
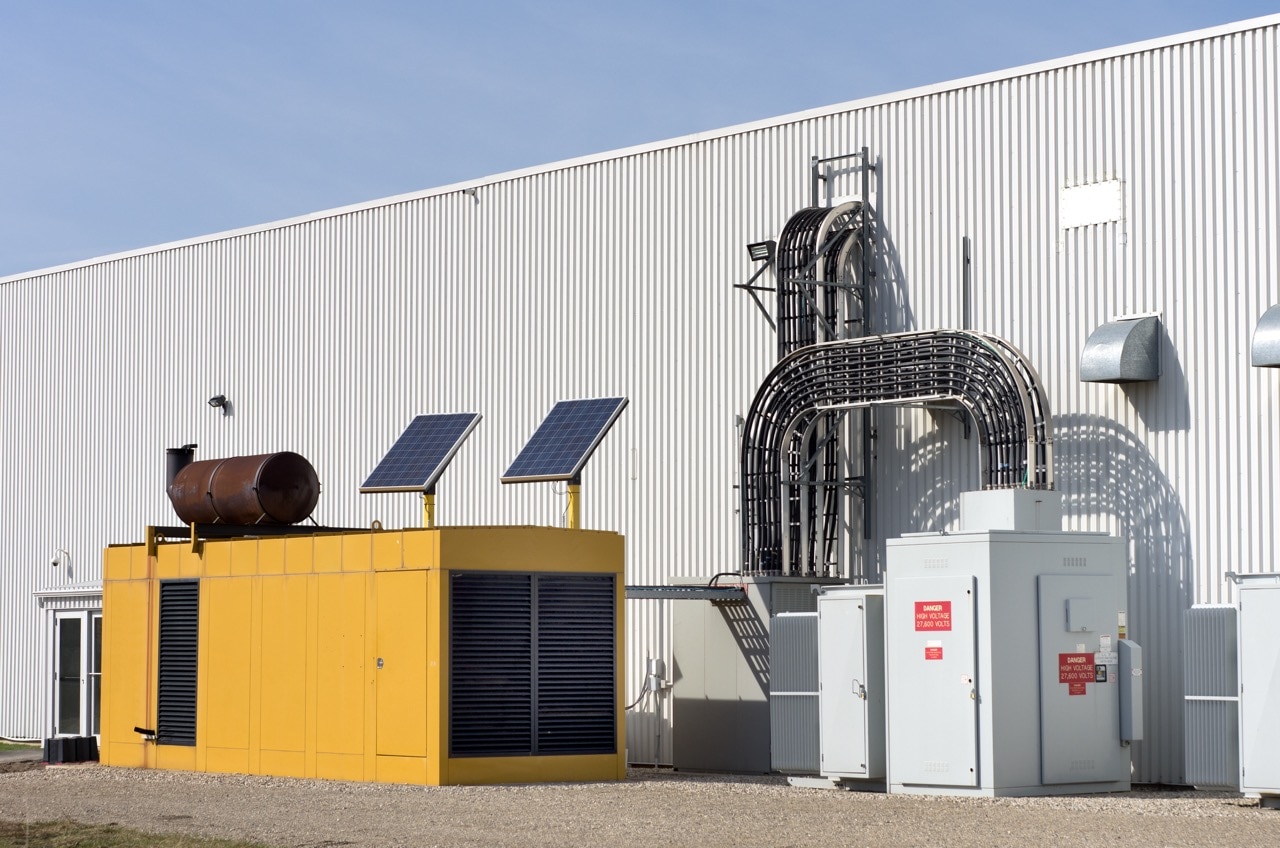
Electric Power Generation
Whether you manage standby generators or large-scale power assets, Monico delivers real-time data acquisition and condition monitoring solutions that improve uptime, efficiency, and regulatory compliance in power generation.
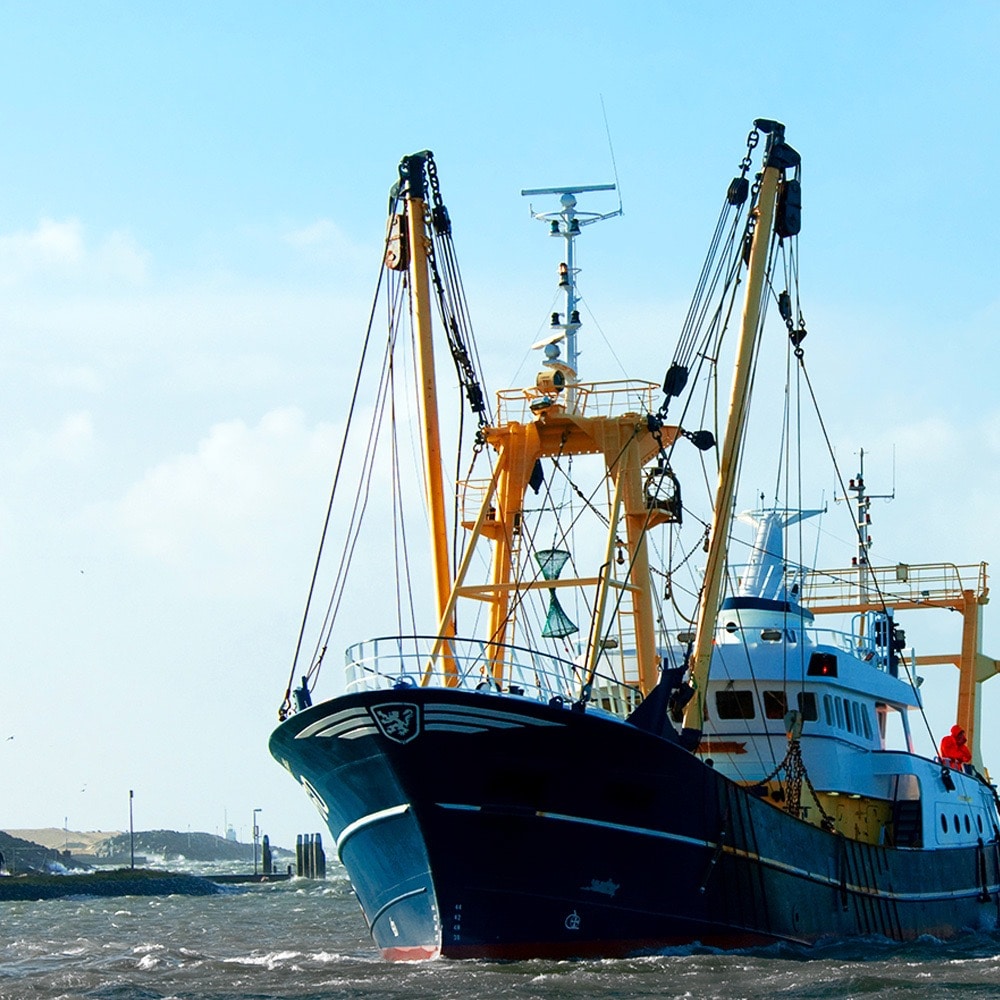
Marine
Monitor engines, propulsion systems, and onboard power assets from anywhere. Monico’s marine-grade solutions are trusted for remote diagnostics, data logging, and integration with enterprise platforms—even in challenging offshore conditions.